The Director-General of COTEC Portugal argues that in a 4.0 environment the director must undertake the role of “process orchestrator” and that immobility will be the greatest risk for the present industrial revolution.
Managing in 4.0 will surely be different. What changes will it be necessary to make in the leadership of companies (in terms of specific skills) for this to happen successfully?
In the era of automation and artificial intelligence, management has reached a turning point: it will continue to be a discipline whose principles will remain relevant but with purposes applied to a very different context. In an organization in the early 20th century, a manager was someone who was “responsible for the work of subordinates”, a “boss”; management was understood as a concept equivalent to hierarchy and power. This idea still persists in the minds of many people.
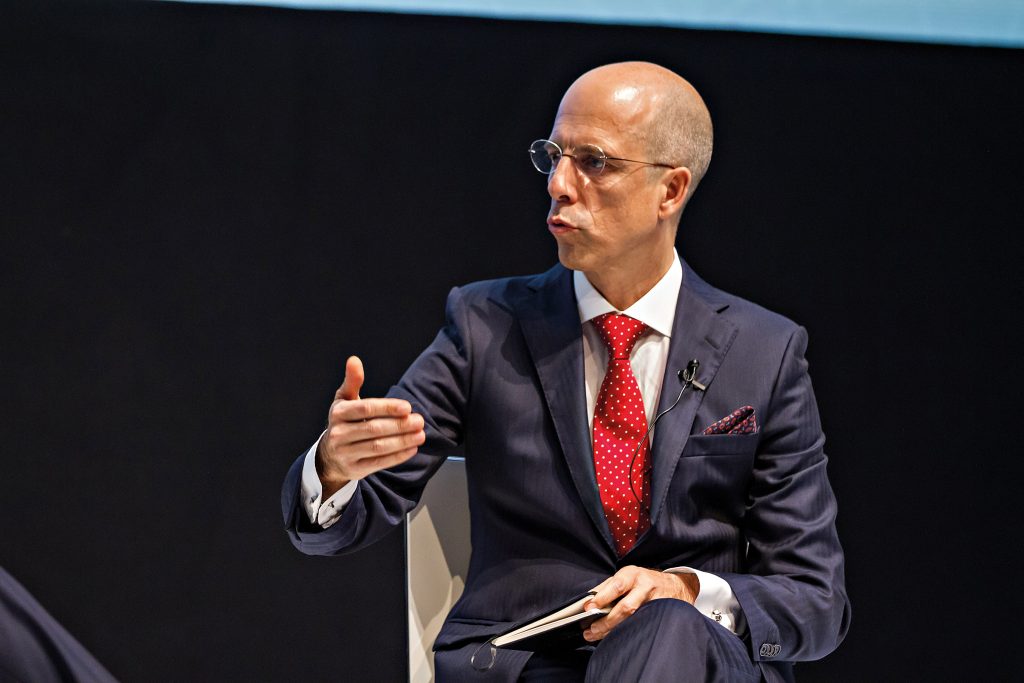
More recently, the concept of manager has evolved into someone “who is responsible for people’s performance”. Revolution 4.0 makes knowledge (or rather, “specialist knowledge”) the essential resource, leaving the others with a set of constraints on what the management function actually is. A manager is seen as someone “who is responsible for applying knowledge and for the respective performance”. The main responsibility of the “Manager 4.0” will be to put the organization’s knowledge into operation, apply knowledge to existing knowledge to reach the desired results.
“PORTUGUESE ENTREPRENEURS HAVE A STRONG DETERMINATION TO OVERCOME OBSTACLES AND A RESISTANCE TO ADVERSITY”
Jorge Portugal
More than an organizer, the manager is the orchestrator of processes that combine the work of humans and intelligent machines in all functions of the organization. But he or she will also have to be the first “destabilizer”, the one that anticipates the need for change, creating the conditions to prevent obsolescence and irrelevance through the organization’s new development cycles. He/she will be the main fiduciary agent of a culture tolerant of constant disturbance and disorganization, abandoning what is familiar, comfortable, established. To succeed in making knowledge productive – in tools, processes, products, in knowledge, at work – the manager will have to obsessively fight for conditions that favour the organization’s decentralization, creating the necessary dose of involvement, trust and motivation at all levels of the organization and from all its members.
Only then will decisions be sufficiently quick and have the necessary proximity to the market, to performance, technology, changes in society, to regulation, environmental conditions, all of which are opportunities to innovate.
How will the transformation change the profile of Portuguese SMEs? And what about our production system?
The convergence between physical and digital resulting from information and communication technologies creates new possibilities in the management of the entire value chain. First, it increases the intensity of information flows at all levels of the value chain, making it possible to place the appropriate information in a timely manner at all points where it is needed and thus generate, over time, useful and valuable practical knowledge to improve management decisions and processes.
Second, it enables “real-time” collaboration between suppliers, partners and customers, a determining factor for eliminating the waste of resources, creating predictability and improving planning, anticipating and preventing incidents, simulating optimizations, reducing production cycle time and improving quality and the customization of the result. The organization of predominantly familiar SMEs, their model of competitive specialization – their agility, flexibility, speed – are intrinsic advantages which are enhanced and defended by the adoption of 4.0 technologies. On the other hand, relevant weaknesses persist: proximity to the end customer, a return from the application of knowledge and the culture of collaboration.
How can we make the leap from where we are today (mid tier among European peers) to the leaders’ group?
First, stimulate technological experimentation, expanding the group of companies that have direct contact and experience with 4.0 technologies and generating opportunities for more innovation. Second, equipped with adequate information on the potential of automation, implement a national Qualification strategy, with the joint responsibility of Companies, workers and the State, aimed at all professional functions in all relevant economic activities, by mapping individual requalification needs and respective professional transition paths. Finally, reinforce support for companies with the greatest potential for future growth through technological transformation and the principles of the business model.
“TECHNOLOGICAL ADVANCES WILL REQUIRE A LONG TERM VISION IN INVESTMENT PLANNING AND A FIRM EXECUTION FROM COMPANIES”
Jorge Portugal
Where are the main obstacles to this revolution in Portugal? And, on the other hand, what potentials and strengths do we have that will give us an advantage?
Portuguese entrepreneurs have a strong determination to overcome obstacles and resist adversity. In very demanding macroeconomic circumstances, they have demonstrated strategic intuition, organizational agility, ingenuity in investment and the ability to adapt to market conditions. There is still a risk of overconfidence in their own capacities, underestimating the impact of scale or the speed of change, the knowledge gaps and how to fill them, and the lack of collaboration to access vital resources that they do not have nationally. Undoubtedly, the greatest risk will be that of immobility, whether it is because the technological implications for business and people are not understood or are undervalued, or because the justification, strategy or means to find a new investment cycle that ensures future competitiveness cannot be found.
In a country where capital is not plentiful, how do you finance change? And how do you get it to be transversal? Isn’t it, from the outset, a race won by the largest companies and those that are most technologically advanced?
Financing for innovation cannot and should not be a constraint on companies of any size. Therefore, conditions must be ensured so that those with less financial expertise and less access to information are not hindered. There is a need to reduce knowledge and access gaps and minimize information asymmetries between demand and supply. If we look at practices in other countries it shows that there is room for improvement, reducing the technical complexity of the instruments, increasing the transparency of access to processes, giving visibility to eligibility criteria and reducing unnecessary bureaucratic burdens. It is possible to achieve a better articulation between public instruments and private sector instruments, e.g. in terms of credit, guarantees and counter-guarantees. The financial sector will be able to improve information on the instruments available, the preferential guidance for understanding the innovation process, and the broadening of risk analysis skills, including the project, the stage of the innovation cycle and the company’s technological maturity. In this regard, COTEC has worked with its associates in the banking sector to include maturity indicators for innovation in the risk assessment of projects.
And what contributions can the strategy make to the biggest challenges currently facing the planet – climate change?
Most of the problems generated by the productive and industrial consumption model can be solved using available technologies. It will be possible, from a technological point of view, to think of a new industrial model operating at low carbon, which is less demanding on material resources, more efficient, with less waste and with durability of products and less environmental impact at the end of life. But technology is not enough. An EU 4.0 regulation is needed, with technical measures and appropriate economic and tax incentives (and disincentives) to stimulate the desired behaviour of economic agents and accelerate the transition. On the other hand, it is necessary to avoid that excessive political voluntarism that puts European companies at a disadvantage compared to their competitors who do not adopt the same environmental quality standards.
How do you transfer knowledge to tangible things? And how do you protect that same knowledge in a world of increasing wars for intellectual property?
The connected economy is an economy of digital services, distributed in a context and customized. Physical products are the vehicles for supporting and providing these services. Knowledge is not only incorporated in the development and production of the product, but it is generated and applied to improve its functioning throughout the life cycle. In this specialized knowledge of the relationship with customers, companies have an essential business asset and source of competitive advantages. To defend these advantages, it is necessary to understand and take advantage of the regulatory environment, but also have strategies that identify, assess and mitigate the internal and external risks that hang over key assets. Preparation and prevention are crucial.
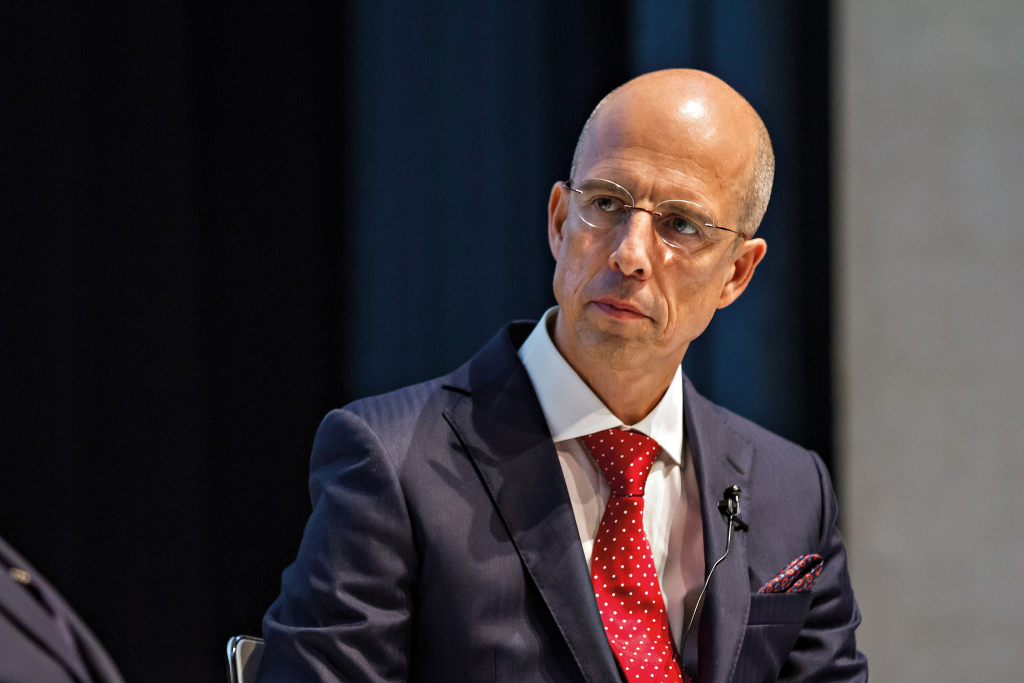
Does the fact that we are in a time of economic boom make it easier to convince companies to develop the necessary investments for digitalization? How can this be done in the event of a crisis?
In view of the succession of crises, Portuguese companies have had no alternative but to invest even when the outlook was not the most favourable or most certain. The economic cycle in recent years has stimulated a greater propensity to invest in digitalization. The changing demands of the market and technological advances will require companies to have a long-term vision in the planning and programming of their investments and a firm and disciplined execution of this plan, which will have to be independent of the level of uncertainty generated by the phases of the political and economic cycles.
Which main axes will mark the next phase in the Industry 4.0 Programme? How do you expect the Portuguese business sector to be at the end of this phase?
The second phase of the Industry 4.0 Programme will be based on three vectors: Generalize, Empower and Assimilate. In the first, it is about stimulating the sharing of knowledge, experiences and advantages among the economic sector as a way to stimulate the broad transition. In the second, align the knowledge of the workforce, allowing companies to access the necessary resources and the creation of inclusive and quality jobs. Finally, supporting companies with the potential for innovation and growth in investment and technological scale-up for the transformation of business models and thus remain competitive. The expectation is that the business sector and in particular Industry, has identified opportunities to invest and make the most of technological possibilities, evolved management skills, developed new business processes, preserved and expanded competitive advantages, achieving greater integration in global value chains, increasing the volume and export value and increasing the environmental sustainability of its production and consumption.
Developed in partnership with:
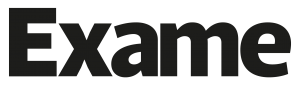